TPMS Heat Exchanger
A functionally generated 3D printed heat exchanger
Objective: Design a heat exchanger that makes use of Triply Periodic Minimal Surfaces (TPMSs), that mitigates the high pressure losses usually reported with these designs
Outcome: Developed several Python scripts to modify implicit TPMS functions to replace baffles and reduce pressure loss
Skills: Python, applied math, heat transfer, CFD (OpenFOAM)
This is a personal project mostly undertaken outside of school. It is ongoing.
Background:
Heat exchangers are ubiquitous across every field of engineering. Academic research indicates that TPMSs can make fantastic heat exchangers due to their continuously curved geometry, large, shared surface area, and natural mixing promotion. Building on research I encountered while working with TPMSs for a different purpose (see: Gyroids), I wanted to see if I could develop a heat exchanger that makes use of these interesting surfaces.
With 3D printing, it’s possible to create geometries that would be impossible through any other means, and adding intricate details to a design no longer increases manufacturing cost. For example, with this heat exchanger, I can functionally (read: smoothly and continuously) change any parameter such as wall thickness, relative volume of the domains, or unit cell size, as a function of X, Y, and Z coordinates. If a reliable heat exchange model could be developed, I could also change parameters based on any thermodynamic property of the working fluids. This could potentially unlock more compact and efficient heat exchangers than are currently possible. Industries such as aerospace and automotive, where size and weight of components are critical, would benefit from these designs.
3D printing is the only way to produce a TPMS (apart from maybe casting certain geometries). The metal 3D printing industry has suffered financially over the past few years due to overhyped prospects; 3D printing requires a very expensive machine and highly trained operator and is fairly slow (similar to machining parts, one of the most expensive metalworking processes). Most parts that can be made through alternative means, especially mass-produced ones, are probably best made using those other means. However, making a conventional brazed plate or shell and tube heat exchanger is also slow and intensive, making heat exchangers pretty expensive anyway. I believe if effective heat exchangers could be developed that require 3D printing, the cost could be justified.
One interesting application for these surfaces is the handling of working fluids at high pressures, e.g. sCO2/R-744 applications. TPMSs are remarkably strong due to their internal interconnectedness and lack of corners to concentrate stress (this was the original reason we were researching them at the Hixon Lab).
What I did:
These surfaces were generated through Python scripts I wrote. They use a numPy meshgrid as a coordinate system, and then evaluate the TPMS level set function across the whole meshgrid to produce a scalar field. The scalar field is then converted to an STL using the marching cubes algorithm. This approach allows for more flexibility in implementation than if industry-standard software was used. For example, I have eliminated the flow-disrupting baffles usually used to separate the working fluids at the inlets/outlets by gradually phasing each subdomain in/out using sigmoid functions (see Yang et. al. paper below, who pioneered this method for tissue engineering), something I believe industry-standard software cannot do.
I believe this approach allows for greater optimization and can be used to reduce the high pressure losses usually reported in the literature. I’m planning to develop a model to better characterize its performance, and once satisfied, have one 3D printed out of metal.
Some conjugate heat transfer simulations were conducted in OpenFOAM. These simulations are more demanding than my computer can handle, so I don’t really trust these results because I had to downsample the mesh quality and the STL file significantly.
Further reading:
Numerical and experimental investigation of the gyroid heat exchanger - ScienceDirect
High performance, microarchitected, compact heat exchanger enabled by 3D printing - ScienceDirect
Review of Triply Periodic Minimal Surface (TPMS) based Heat Exchanger Designs (purdue.edu)

OpenFOAM simulation showing the transfer of heat between regions through a solid interface. This simulation was mostly done to develop my CFD skills for future work. Future iterations of this heat exchanger will better promote counterflow.
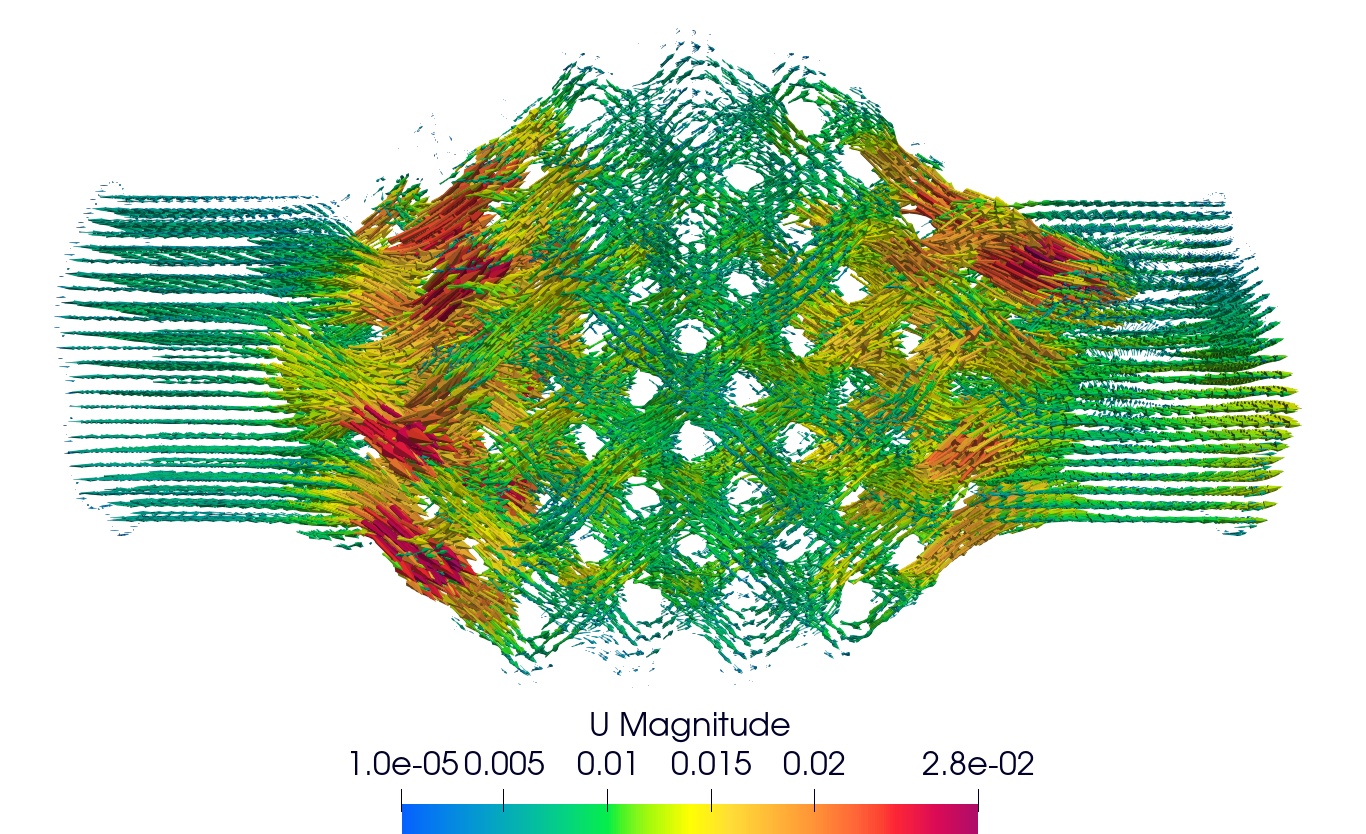
Velocity magnitude showing flow constriction at the inlets and outlets (OpenFOAM). Future iterations will avoid this.

A plastic 3D print of one of my heat exchangers. This one uses CAD geometry for the fittings/outer shell, which I found a way to integrate into my scalar field approach without sacrificing the smooth transition.
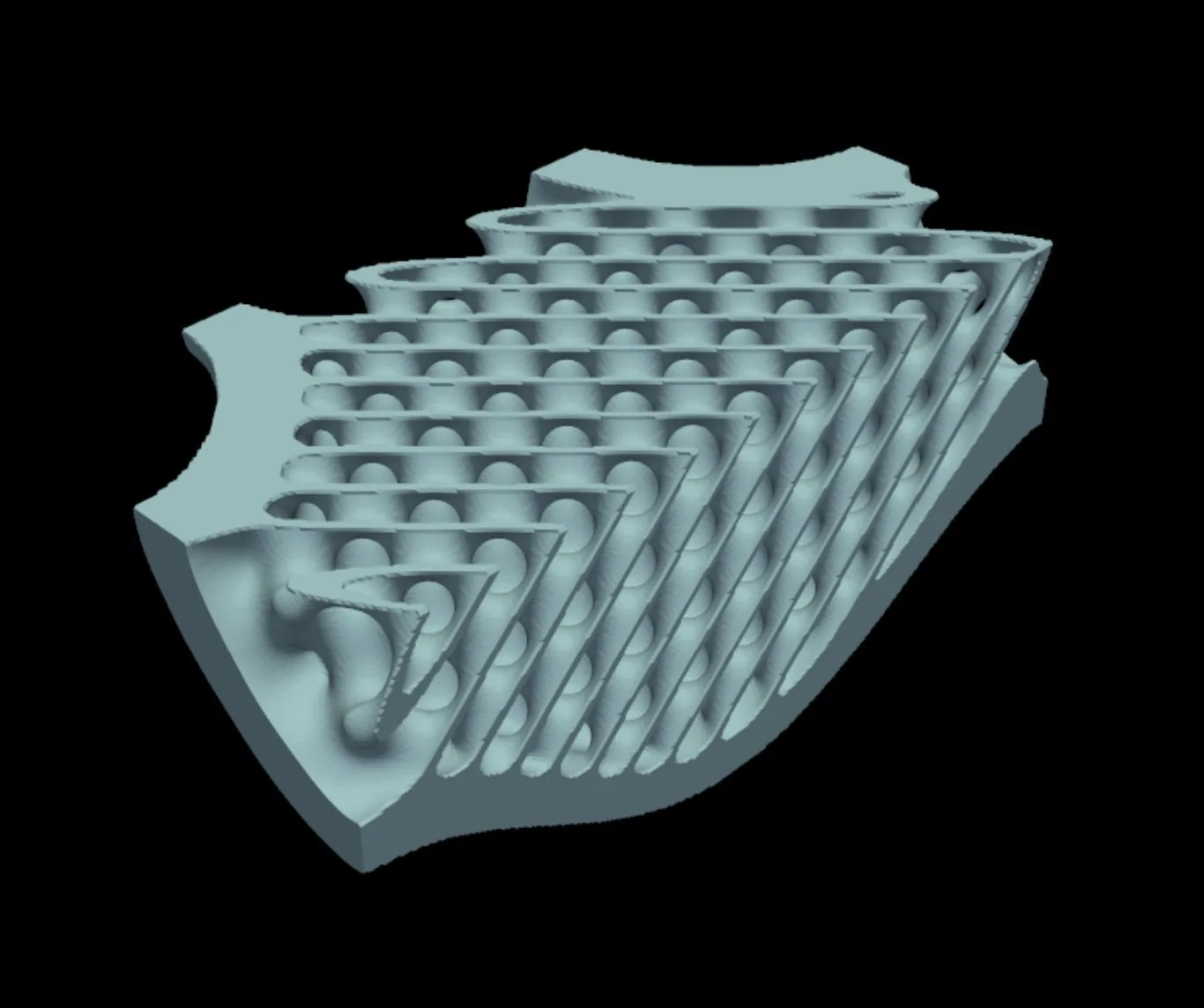
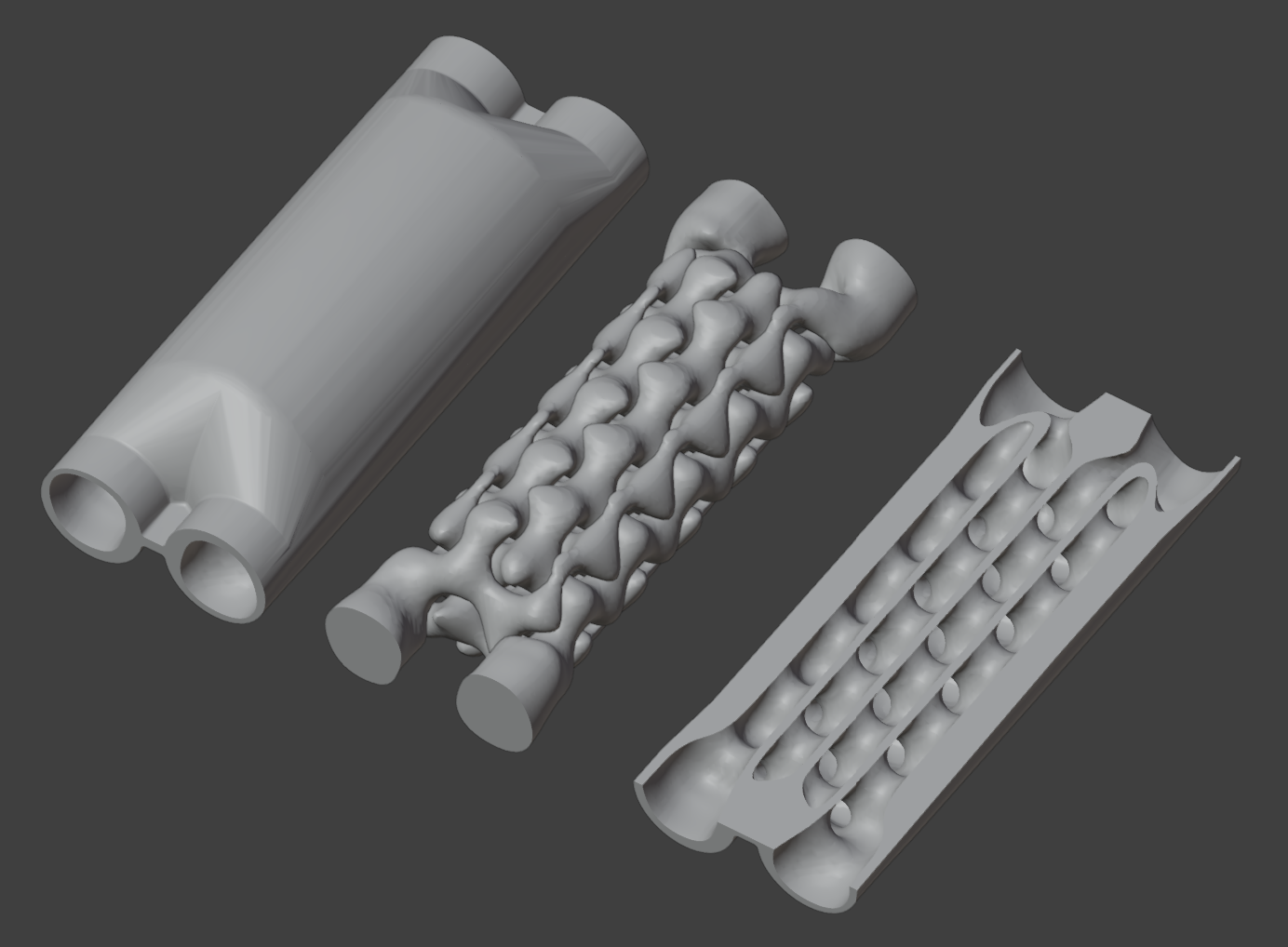
An example of using a non functionally-defined mesh (e.g. this heat exchanger shell made in SolidWorks) to constrain the TPMS, while still maintaining the smoothed boundary between the two.
A fully functionally defined heat exchanger, mesh edited into a counterflow arrangement.
The two separate fluid volumes. Conventional HXs use baffles to separate them at the inlet/outlet, rather than gradually phasing each subdomain in/out
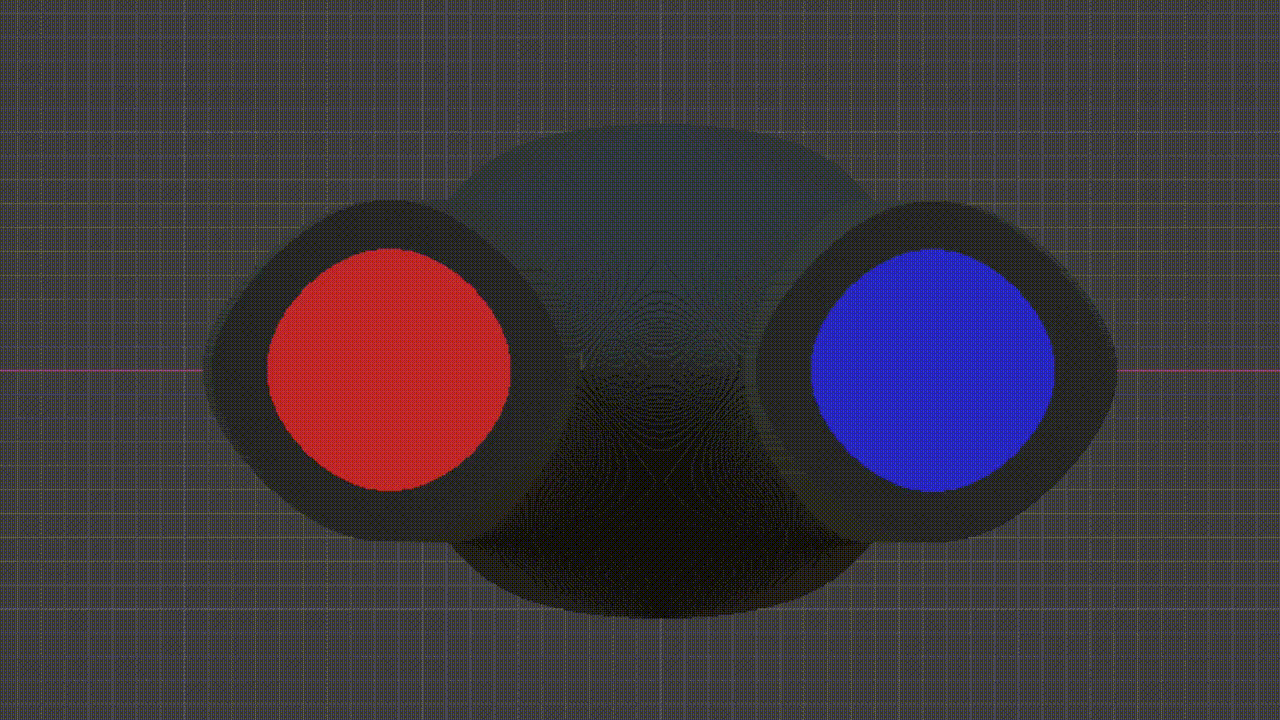
A cross sectional sweep. Please ignore the Blender boolean errors, I’m working on it.